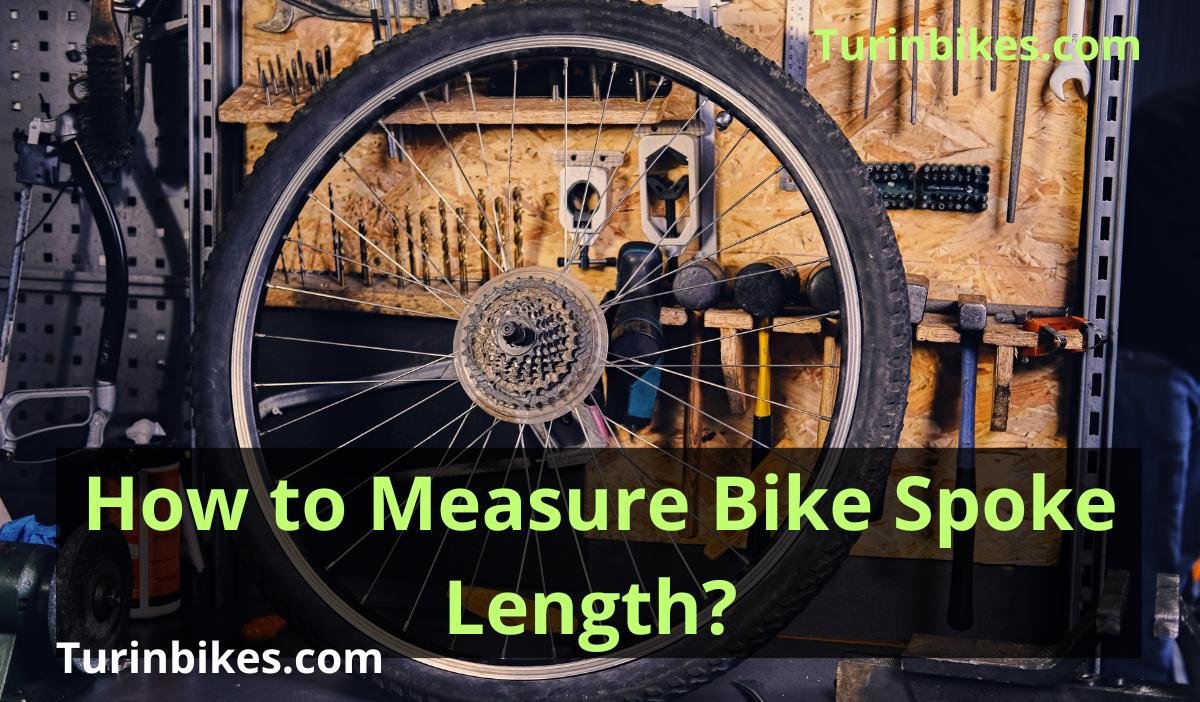
Spoke length is a crucial factor for properly building and maintaining bike wheels. But how do you determine the ideal measurement for your hub and rim combo? When replacing damaged spokes or replacing a wheel, getting the size right prevents problems down the road. While spoke length calculations can seem complex, having the right tools and technique makes the process straightforward. In this beginner-friendly guide, we’ll walk through how to Measure Bike Spoke length and choose spokes for your road, mountain, or custom wheel build. You’ll learn the key reference points and formulas to confidently determine the optimal spoke length needed for a safe and balanced wheel. Let’s delve into demystifying spoke measurement once and for all!
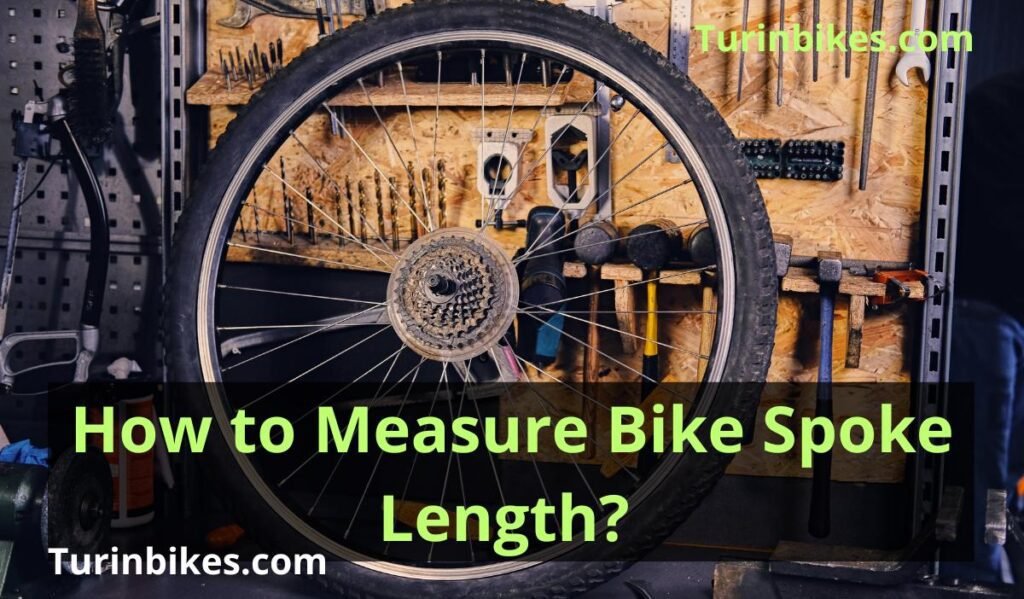
What are Bike Spokes?
Bike spokes are slender metal rods that connect the central hub to the outer rim of the wheel. Spokes provide structural support and integrity to the wheel so it can withstand the forces of riding and handling the weight of the bike and rider.
Spokes are precisely manufactured and installed to have uniform length and tension. Determining the correct spoke length is crucial for proper wheel function. Spoke calculators can recommend the ideal spoke length based on the number of spoke holes in the hub and rim, wheel diameter, and other factors.
Understanding The Role Of Spokes In A Bicycle Wheel:
Bicycle spokes are made with thin metal rods that connect the central hub to the outer rim, providing structure and support for the entire wheel. Spokes carry the weight of the rider from the hub, where it is concentrated down to the rim in a more distributed manner. They also absorb impacts from bumps in the road or trail to prevent them from jolting the wheel. Spokes must maintain adequate tension to perform these key functions properly. Without taut spokes, the wheel would collapse under the forces of riding.
Different Types Of Spokes And Their Characteristics:
There are different types of bike spokes designed for different riding needs. Road bikes often use narrow aero or bladed spokes that are flattened to reduce wind resistance. Mountain bike spokes are thicker and stronger to withstand rigorous off-road riding conditions. Spokes also vary in materials from stainless steel alloys to aluminium or titanium. Butt end spokes that are thicker at one end provide optimized strength. Choosing the right spoke design and material ensures they meet the demands of the intended riding style.
Importance Of Proper Spoke Tension For Wheel Performance:
Proper spoke tension is absolutely critical for wheel performance and preventing common spoke problems. Tension should be high enough to suspend the weight of bike and rider without excessive strain on individual spokes. If tension is too low, spokes can loosen, wheels lose true, and spokes fatigue and break more easily. Spokes on the same wheel must have uniform tension to avoid instability. Tension meters help measure and equalize tension during wheel builds and maintenance.
Common Issues With Bike Spokes And How To Identify Them:
Damaged and worn spokes manifest in several ways. Corrosion near spoke nipples can lead to breakage. Loose spokes cause the wheel to wobble and go out of true. Broken spokes require immediate replacement to regain wheel strength. Any spokes bent out of shape also require replacement. Regularly inspecting each spoke can identify issues before total wheel failure occurs. Catching problems early preserves the wheel.
Tips For Maintaining And Prolonging The Life Of Bike Spokes:
Check spoke tension monthly and turn nipples incrementally to maintain even tension. Replace any broken or damaged spokes promptly with the correct new spoke length. Apply corrosion inhibitors near spoke threads. Clean grime from spokes with mild soap and water. Store wheels away from moisture and extreme temps. Equalize tension across groups of spokes to share strain. Quality builds, and regular maintenance will get the longest life from your bike’s spokes.
How to Measure Spoke Length:
Step-by-step guide to measuring bike spoke length:
To accurately determine spoke length, we’ll calculate the measurements from the hub flange where the spokes attach, to the rim where the spoke ends connect. This practical way to measure ensures we get the correct size spoke needed for building a bicycle wheel or lacing the wheel properly. We’ll measure from the inside elbow of the J-bend in the spoke to the center of the spoke holes on the rim.
Factors to consider when determining the appropriate spoke length:
When measuring spoke length, consider the diameter of the hub flange, diameter of the rim, number of spoke holes, lacing pattern, and whether it’s the rear wheel or front wheel. These factors all determine the correct length of spokes required for building a balanced bicycle wheel.
Using a spoke length calculator for accurate measurements:
Online spoke calculators allow inputting the hub model and dimensions along with the rim ERD to automatically calculate spoke lengths. This saves time and gives an accurate starting point for the length of spokes needed for spoking the wheel properly.
Understanding the role of rim and hub in spoke length calculations:
The distance from the hub-spoke holes to the rim’s centre is the key measurement that sets spoke length. Measuring this effective rim diameter (ERD) sets the length required for correct tension from the hub flange to the J-bend at the rim.
Final calculations and adjustments for spoke length:
The initial spoke length measurement may need minor adjustments during wheel building to account for factors like spoke thickness and desired wheel dish. But the measured length from the hub flange to rim hole centers gives the optimal starting point for calculating spoke lengths.

Tools and Techniques for Measuring Bike Spokes
Using a spoke ruler or caliper for precise measurements:
A spoke ruler with millimeter markings is the best tool for precisely measuring spoke length. Place the threaded end at 0mm and measure to the elbow to get the correct length. Digital calipers also work well for getting highly accurate spoke-length measurements.
Alternative methods to measure spoke length without specialized tools:
If you don’t have a spoke ruler, you can use a regular measuring tape, mark the spoke at the right flange, then measure from the mark to the end to determine length. A plain gauge wire with millimeter markings is another DIY option for measuring spokes.
Common mistakes to avoid when measuring spokes:
Some errors, like including the head when measuring or misreading the ruler, can lead to selecting the wrong size spokes. Always measure from the threaded end and double-check your readings. Also, be aware that front and rear wheel spokes often need different lengths.
Recommended tools for building and adjusting bike wheels:
Spoke tension meters, truing stands, dish sticks, and nipple drivers help create even tension and true wheels. Good tools make accurate spoke-length calculation easier and wheel building much smoother.
Understanding the importance of spoke tension and consistency:
Consistent spoke tension ensures wheels stay true and evenly distribute strain. Measuring and adjusting tension on newly laced wheels helps identify any spokes that may need shortening or lengthening to achieve uniformity.
Choosing the Right Spokes for Your Bike Wheel Build
Factors to consider when selecting spokes for different types of bikes:
The riding purpose affects spoke choice – wider 35mm+ rims for downhill require thicker spokes than a road bike. Consider the rim and hub dimensions to determine the right length. Measure precisely as 1mm variance in spoke length can impact wheel true.
Importance of spoke diameter and strength for specific riding requirements:
Thicker spokes around 2.5mm are best for absorbing impacts on mountain bikes. Thinner spokes down to 1mm suit lightweight road bikes more optimally. Consider spoke material too – stainless steel spokes handle torque well for powerful e-bikes and hub motors.
Lacing patterns and their impact on wheel performance:
Radial lacing is optimal for front wheels, offering a stiff but compliant ride. Rear wheels benefit from 2-cross or 3-cross lacing to better handle torque without going out of true. The pattern interweaving spokes affects wheel strength.
Understanding spoke nipple types and their compatibility with spokes:
Brass nipples are common but aluminum weighs less. Ensure nipple holes fit the spokes being used and calculate the extra length needed for long nipples. Use rim tape to avoid sharp nipple ends puncturing tubes.
Expert tips for building a durable and reliable bike wheel:
Accurately measure your hubs and rims, then calculate the ideal spoke length. Tension spokes evenly in increments before stress relieving the wheel. Use spoke prep fluid to prevent broken spokes seizing. True the wheel and do final micro adjustments to length for perfectly dished wheels.
Final Thoughts:
Selecting the ideal spoke length is fundamental to building a wheel that’s durable, balanced, and tailored to your bike. While measuring spokes and calculating lengths may seem complicated at first, having the right tools and techniques makes the process straightforward. Always double check your numbers, consult spoke length calculators, and take your time during the build to lace each spoke at the proper tension. Precision and attention to detail is key. With practice, you’ll be able to confidently measure and replace spokes to keep your wheels rolling for thousands of miles. Proper maintenance along the way will maximize performance and riding enjoyment. So, don’t shy away from learning this integral skill. Perfectly measured spokes lead to perfectly spinning wheels and a smoother, more responsive ride.
Can I Reuse Old Spokes When Building A New Wheel?
It’s generally not recommended to reuse old spokes when lacing a new wheel. Over time, spokes get fatigued and stressed, which compromises strength. New spokes specially sized for the new rim and hub ensure optimal durability.
Is It Possible To Measure Spoke Length Without Removing The Wheel?
Yes, you can measure spoke length in situ by marking the initial start point, counting the threads and measuring to the elbow. But removing the wheel allows more precision in measuring from the hub flange.
How Often Should I Check And Adjust Spoke Tension?
Test spoke tension at least every 1-2 months to check for looseness. Any loose spokes should be tightened before they cause the wheel to go out of turn. This regular maintenance prevents problems.
What Are The Consequences Of Using Incorrect Spoke Lengths?
If spokes are too short, they will over-stress the wheel. Spokes too long will have inadequate tension, leading to flex and looseness. Either scenario can lead to wobbles, cracks, and spokes breaking.
Why Is It Important To Have Evenly Tensioned Spokes?
Consistent tension shares the strain equally across all spokes. This prevents fatigue and damage from concentrating in certain spots. It also helps the wheel run true without deviation.
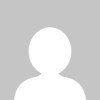
Meet Sachin Kumar, an avid cyclist and bike enthusiast with a passion for two-wheeled adventures. At our Turinbikes site, Sachin shares expert insights, thrilling ride experiences, and tips for fellow bike lovers.